Efficient recycling and expanded use of plastic waste streams
Eight Fraunhofer Institutes have developed new solutions for waste management and the circular economy of plastics in the lighthouse project "Waste4Future". With their expertise, they are improving aspects such as recycling, sorting, recipe development, utilization paths and the minimization of waste streams. In particular, this makes it possible to use waste containing plastic that was previously incinerated. The results have now been presented to industry representatives at a final meeting.
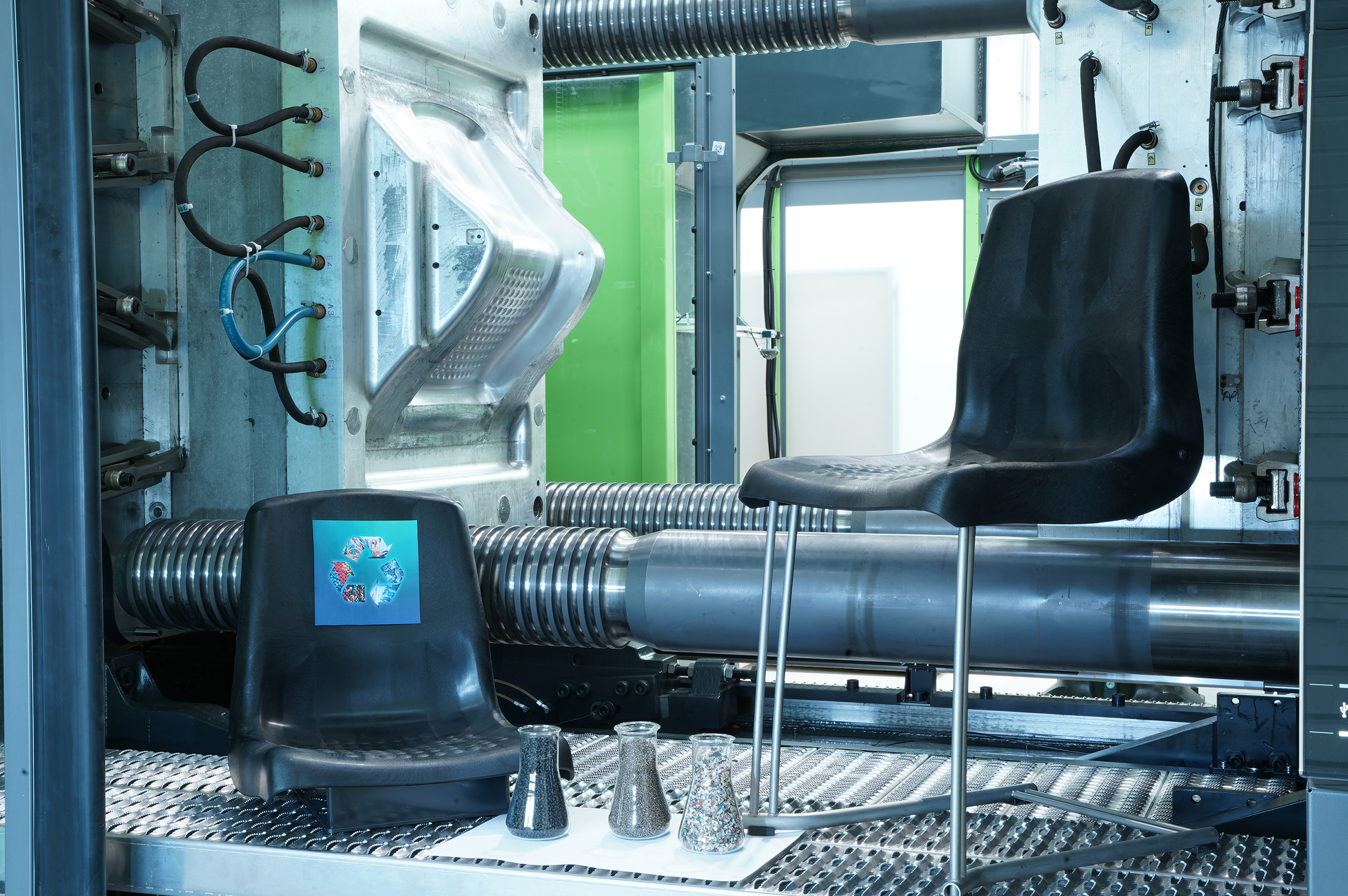
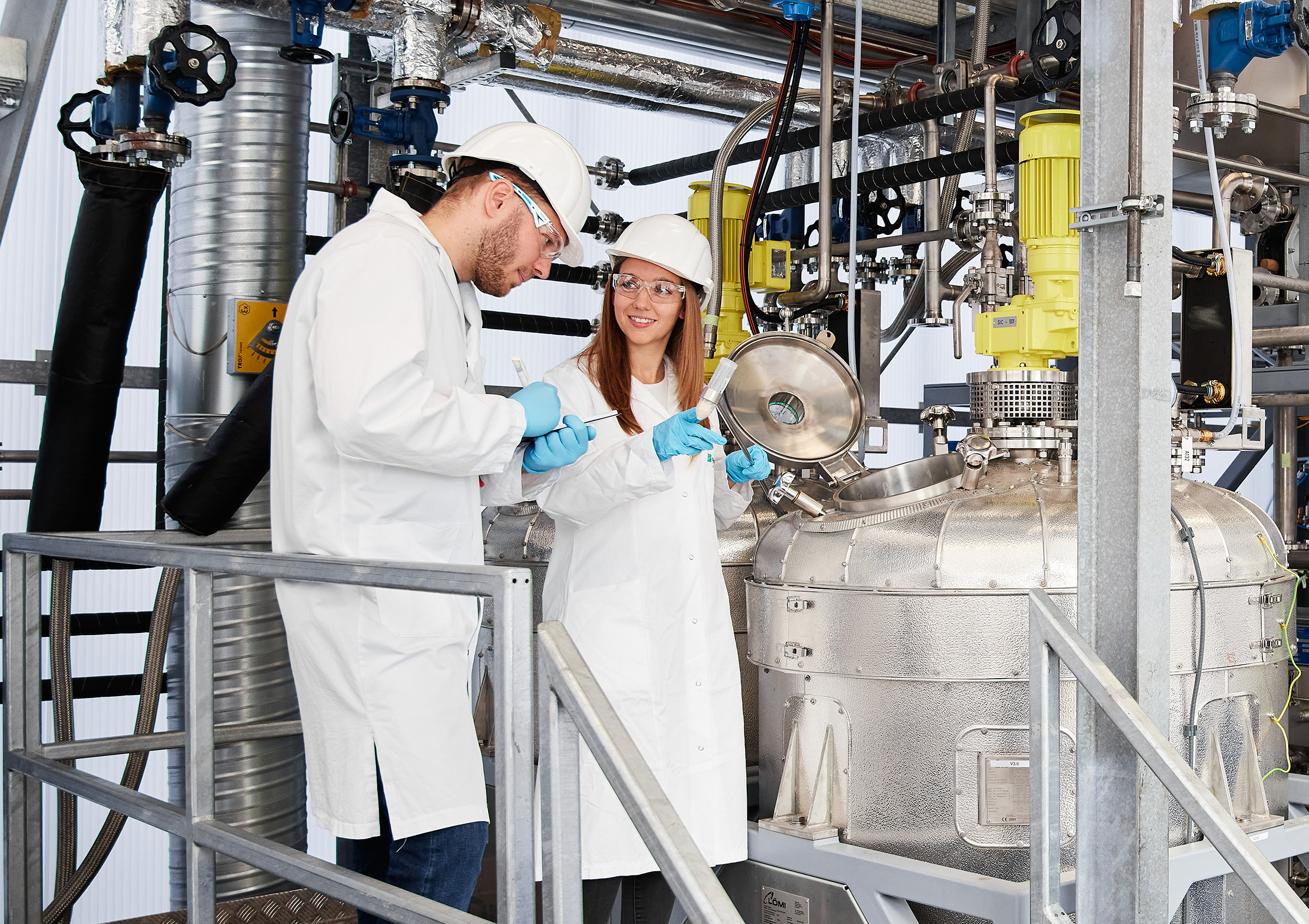
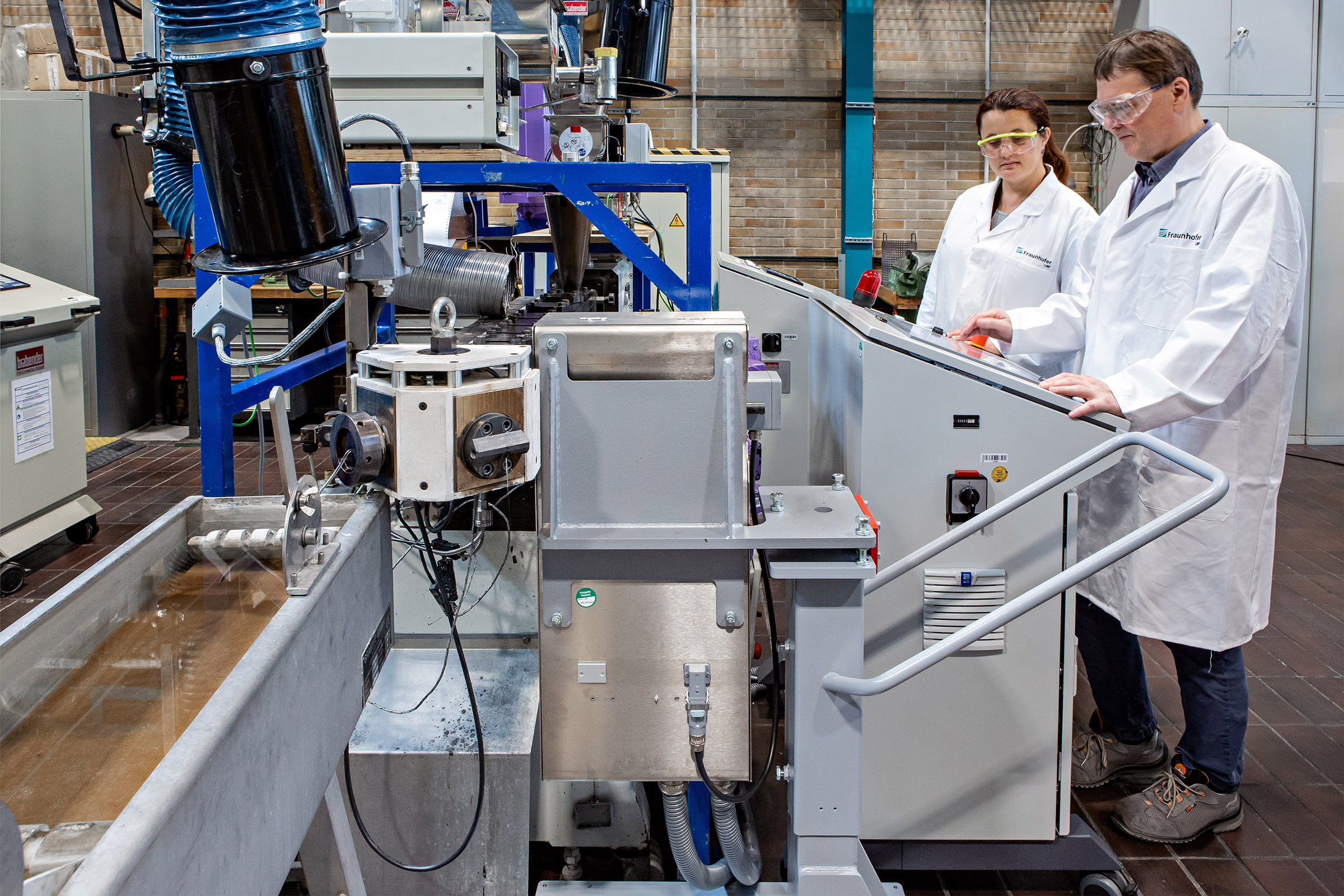
High-performance plastics are among the world's most important materials and make many applications possible in the first place, bringing considerable benefits for industrial use as well as for our everyday lives. However, they are usually made from fossil raw materials, which results in corresponding CO2 emissions. In addition, more than 6 million tons of waste containing plastics are produced in Germany alone every year, around half of which is currently still incinerated instead of being recycled.
"The approach of considering the carbon contained in plastic as a resource and using it further is therefore an obvious one. The prerequisite for establishing such a circular economy is to better identify carbon-containing components in waste, to recycle them more effectively and to turn them back into high-quality raw materials for industry. With our combined expertise, we have found individual and innovative solutions for very differently composed waste streams in the lighthouse project," says Prof. Dr. Erica Lilleodden, overall project manager of "Waste4Future" and Director of the Fraunhofer Institute for Microstructure of Materials and Systems IMWS, which was in charge of the project. The Fraunhofer experts focused in particular on the use of plastic waste that could not previously be recycled and set the six research priorities of evaluation model, sensor technology, sorting technology, material recycling, chemical recycling and formulation development.
Focus on recycling of polyamide
To demonstrate the new possibilities, they produced a chair shell from recycled polyamide. The plastic was automatically sorted out of a waste stream, subsequently processed and then injection molded. The component behavior was compared with virgin material and other available recyclates. The result: the recycled seat shell is competitive in all key aspects. "We focused on polyamide because there is a high demand from the automotive industry in particular and the demand will increase in the coming years due to strict regulation," says Prof. Dr. Maik Feldmann, Technical Project Manager of "Waste4Future". "With the demonstrator, we in the consortium were able to trace the entire path from the complex waste stream from a shredder light fraction through high-quality recyclates to the new product and show in how many areas we have made progress together."
Of particular note is the development of a basis for a holistic model that allows (real-time) evaluation of (plastic) recycling processes according to ecological and economic criteria. The model enables statements to be made about the quality of a waste stream and how its individual components can be recycled with the highest possible quality. "By creating digital twins of processes and materials, we have created an opportunity for interaction between the real and virtual worlds," says Dr. Gert Homm, head of the "Entropy-based evaluation model" sub-project. A sorting demonstrator (multi-sensor system with AI-based data evaluation) was also developed and the fundamental suitability of THz sensor technology for sorting black plastics, which has hardly been possible to date, was demonstrated, although it still needs to be further developed for sorting real waste fractions.
New possibilities for recipe development and chemical recycling
Significant progress has been made in the evaluation of recyclates (e.g. ageing processes) and in formulation development (e.g. additives). For example, online rheology was developed as a rapid diagnostic tool for formulation development, such as the use of process stabilizers in polyolefins and coupler additives for molecular weight build-up in polyamides. In the case of polyolefins, the project team has identified so-called tipping points as a sorting criterion for cascaded processing. The production of high-purity plastic recyclates was successfully implemented using solvent-based recycling. Suitable recycling paths for polypropylene (PP), polystyrene (PS), acrylonitrile-butadiene-styrene copolymers (ABS) and polyamide (PA) from shredder waste were designed and mass balances of highly inhomogeneous waste streams (post-industrial and post-consumer plastic waste) were drawn up.
For chemical recycling (pyrolysis, gasification), the new entropy model enables a holistic assessment of waste streams containing plastics. "We were able to show that gasification and pyrolysis can also be used to recycle polyamide-containing fractions that are no longer mechanically recyclable," says Dr. Jörg Kleeberg, head of the "Chemical Recycling" sub-project. The results form the basis for ASPEN modeling, which can also be used as a basis for the synthesis of completely new plastics.
In all activities, the project partners kept in mind that innovative solutions must not only work in the laboratory, but also be scalable to the needs of industry. Accordingly, the participating institutes used their first-class technical equipment to work on demonstrator and pilot scale in many areas. Dr. Elke Metzsch-Zilligen, head of the "Materials Recycling" sub-project, concludes: "We always looked at the entire system, including the economic evaluation and regulatory framework conditions. The optimizations achieved in sorting, purification, processing of recycled plastics in high quality and identification of suitable recycling paths offer very attractive new opportunities, for example for waste management and the chemical industry, right through to the development of completely new business models."
The institutes involved in the lighthouse project were:
- Fraunhofer Institute for High Frequency Physics and Radar Techniques FHR
- Fraunhofer Institute for Ceramic Technologies and Systems IKTS
- Fraunhofer Institute for Microstructure of Materials and Systems IMWS
- Fraunhofer Institute of Optronics, System Technologies and Image Exploitation IOSB
- Fraunhofer Institute for Process Engineering and Packaging IVV
- Fraunhofer Research Institution for Materials Recycling and Resource Strategies IWKS
- Fraunhofer Institute for Non-Destructive Testing IZFP
- Fraunhofer Institute for Structural Durability and System Reliability LBF
The images may be used free of charge for editorial purposes for reporting on this topic. Use for other purposes is only permitted with the prior consent of the Fraunhofer IMWS.
Last modified: